Recycled silicon powder from end-of-life solar panels can be reused in anti-corrosion coating
Researchers in India have demonstrated a wet chemical process to recover silicon with high purity from end-of-life solar panels, which they used to make functionalized silica nanoparticles. Tests of the processed nanoparticles in anti-corrosion coatings showed a corrosion protection efficiency of 99.5 %, which they said was 200 times lower corrosion rate compared to uncoated silica nanoparticles.

Researchers in India have demonstrated a wet chemical process to recover silicon with high purity from end-of-life solar panels, which they used to make functionalized silica nanoparticles. Tests of the processed nanoparticles in anti-corrosion coatings showed a corrosion protection efficiency of 99.5 %, which they said was 200 times lower corrosion rate compared to uncoated silica nanoparticles.
Researchers in India have demonstrated a wet chemical process to recover silicon material from dismantled end-of-life (EoL) solar panels.
To validate the usefulness of the recovered silicon the scientists produced functionalized silica nanoparticles, which were then used as anti-corrosion coatings in a polymer. Test results showed a corrosion protection efficiency of 99.5 %, which they said is around 200 times lower corrosion rate compared to uncoated silica nanoparticles.
The scientists noted that their facile wet chemical process for recycling EoL panels focused on aluminum back surface field (Al-BSF) type panels because most of the current and future EoL panels will be of this type.
“We demonstrated an efficient, environment-friendly, sustainable, circular economy-driven waste-to-wealth strategy for managing the globally growing EoL solar panel waste streams,” Parveen Saini, corresponding author of the research, told pv magazine. “It was challenging to recover silicon-solar cells that are encapsulated between top and bottom ethyl-vinyl acetate (EVA) polymer sheets, without incinerating the EVA.”
The team used solvents for the EVA removal step, which presented yet another challenge that had to be overcome: preventing the loss of used medium or solvents and subsequent regeneration for reuse.
Recovered cells were exposed to successive chemical treatments to selectively etch out various layers, such as the top silver finger contacts, top anti-reflection coatings, and bottom aluminum contact layer, according to the research. The component materials, such as silicon cells, cover glass, connecting wires, and layers of polymeric were separated to expose the bare silicon wafer. It had a purity of over 99.9%.
Acknowledging that the recovered silicon could not be re-used to manufacture solar silicon, the team decided to use it to make silica nanoparticles, optical grade hydrophilic silica nanoparticles with optimized functionalization.
The team took crushed silicon powder to use as a precursor for the synthesis of the silica nanoparticles, which was processed through chemical functionalization into silica (SNP) and hydrophobic silica (HSNP) nanoparticles in a three-step process. The SNPs and HSNPs were then characterized based on structural, morphological, optical, and spectroscopic techniques.
The HSNPs were used as anti-corrosion coatings and they “significantly” outperformed conventional coatings based on both plain polymeric matrix and uncoated nanoparticles-filled polymer composites. The corrosion inhibition efficiency was 99.5 %, and the corrosion rate was about 200 times lower compared to the uncoated silica nanoparticles-filled polymer coating, according to the team.
The performance was attributed to the ability of the nanoparticles to minimize water absorption and effectively prevent corrosive agents from reaching the substrate.
The research is described in “A facile waste-to-wealth approach for synthesis of functionalized silica nanoparticles from end-of-life solar panel waste for technological applications,” published in Resources, Conservation and Recycling.
The HSNP recovery process has already attracted attention outside academia. “People from the corrosion industry as well as the specialty coating industry have shown interest in the recovery and repurposing,” said Saini.
Looking ahead, the research team intends to scale up and tailor the nanoparticle process by redesigning it – or reducing the steps – to better fit existing value chains and targeted applications. Further efforts are underway towards the “conversion of these particles into industrially useful end products,” said Saini.
The researchers were from the Academy of Scientific and Innovative Research (AcSIR), the CSIR-National Physical Laboratory, and the University of Delhi.
What's Your Reaction?
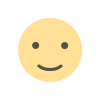
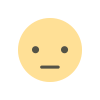
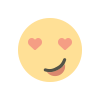
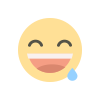

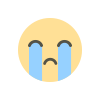
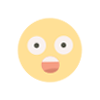