Autowell Technology unveils 0BB tool for multiple silicon PV module technologies
The equipment with a processing speed of up to 10,800 pcs/h can be used to upgrade existing super multi-busbar (SMBB) and multi-busbar (MBB) equipment made by China-based Wuxi Autowell Technology (ATW). It is suitable for tunnel oxide passivated contact (TOPCon), heterojunction (HJT), and back-contact (BC) cell technologies.

The equipment with a processing speed of up to 10,800 pcs/h can be used to upgrade existing super multi-busbar (SMBB) and multi-busbar (MBB) equipment made by China-based Wuxi Autowell Technology (ATW). It is suitable for tunnel oxide passivated contact (TOPCon), heterojunction (HJT), and back-contact (BC) cell technologies.
China-based solar PV equipment manufacturer, Wuxi Autowell Technology (ATW), has launched a busbarless, or zero-busbar (0BB), stringer that is suitable for new and existing customers. It is designed to retrofit legacy ATW super multi-busbar (SMBB) and multi-busbar (MBB) production lines.
Indeed, its latest customer, a 10 GW silicon heterojunction (HJT) manufacturer, is using the technology to upgrade a legacy interconnect process described by ATW in a statement as a “welding prior to adhesive printing” workflow.
ATW noted that it has been developing 0BB technology, which is compatible with tunnel oxide passivated contact (TOPCon), HJT, and back-contact (BC) cell technologies, since 2021. It holds over 120 patents for its 0BB tool, which was commercialized in 2024.
The decision to adopt 0BB is driven by a need to reduce silver consumption while maintaining high yield. “For cell producers, reducing silver paste consumption by 10% lowers manufacturing costs – it's a critical factor in today's competitive solar market,” an ATW spokesperson told pv magazine. “On the module side, the optimized current collection path with finer wires minimizes resistive losses boosting output.”
The 0BB equipment is used for cells that range in size from 156 mm to 230 mm, which are processed at a speed of up to 10,800 pcs/h. String lengths can be up to 1,250 mm, with customization for other sizes available. The cutting groove laser power is 50 W, while the heating laser is 300 W. The tool’s average power is 55 kW and 80 kW peak. It measures 10,750 x 2,500 x 2,650 mm.
The equipment supports “adhesive application followed by curing” workflows, as well as “welding prior to adhesive application and curing” workflows. It is compatible with UV-curable and epoxy-based adhesive systems. Inspection is enabled by charge-coupled device (CCD) cameras. Strip, string, and electroluminescence (EL) inspection equipment is optional.
What's Your Reaction?
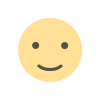
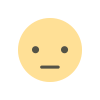
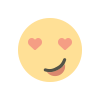
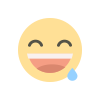

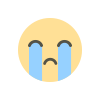
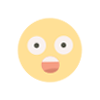