Pultrusion Solutions
When industry leaders, suppliers, OEMs and customers gather in downtown Chicago this May for the North American Pultrusion Conference (NAPC), they’ll discover what’s new in manufacturing, materials and markets. In […] The post Pultrusion Solutions appeared first on American Composites Manufacturers Association.
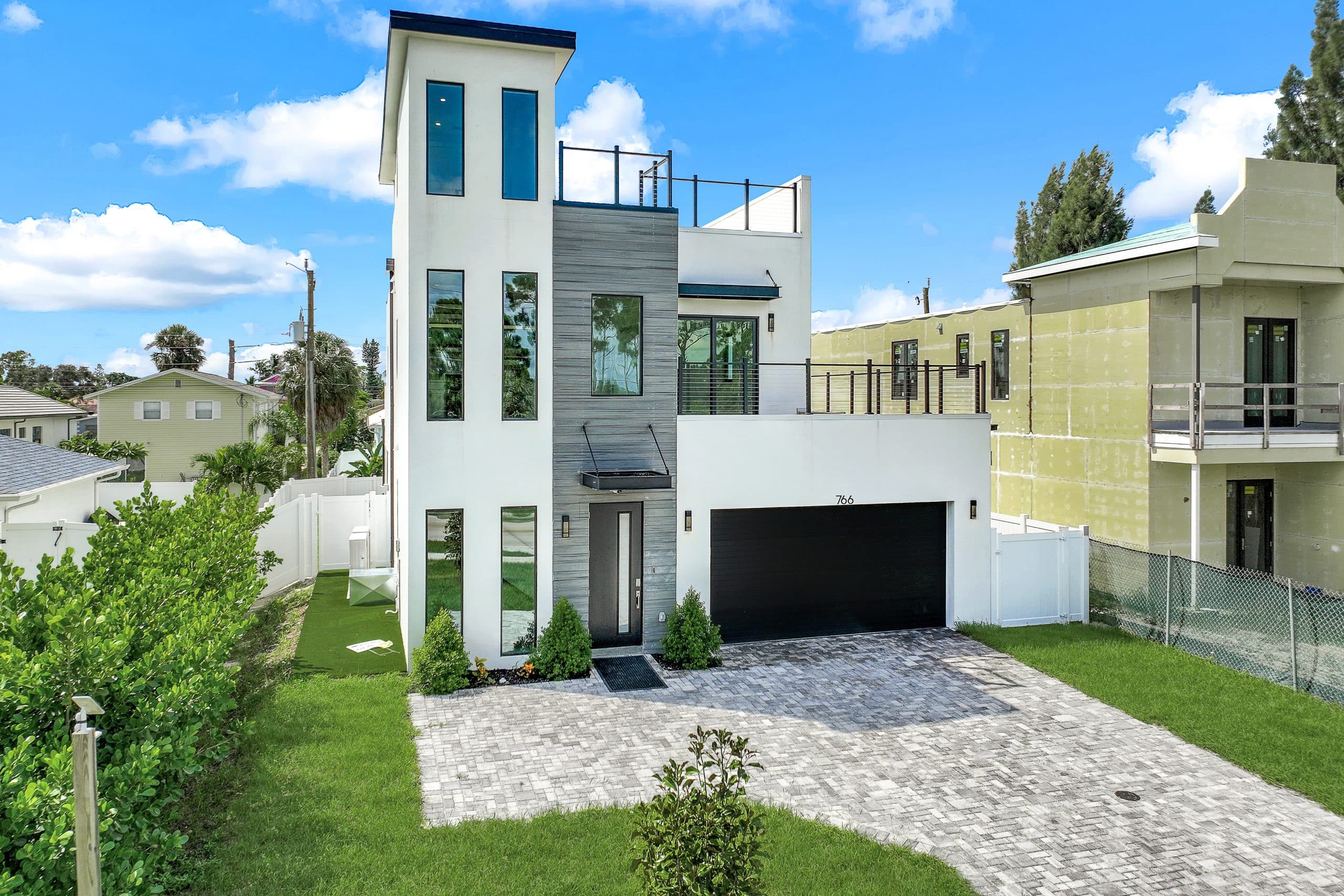
When industry leaders, suppliers, OEMs and customers gather in downtown Chicago this May for the North American Pultrusion Conference (NAPC), they’ll discover what’s new in manufacturing, materials and markets. In this preview article for the conference, Composites Manufacturing magazine caught up with three presenters for a look inside markets where pultrusion is making a mark – construction, transportation and fenestration.
Company: Northstar Technologies Group
Market: Construction
In 2020, Northstar Technologies Group Inc. transitioned from traditional materials to a 100% composite system for its exterior wall panel system. The company’s EXOSHELL wall panels include a Level 1 ballistic-rated GFRP armor plate bonded to a pultruded composite 6-inch C-channel frame assembly that is factory fitted, sealed and fire coated.
The company initially targeted residential construction for the product line, which earned Florida’s High Velocity Hurricane Zone (HVHZ) approval and secured a 250-mph impact rating. A local investor in Naples, Fla., contracted the company to design and construct a one-of-a-kind 3,100-square-foot prototype house featuring the EXOSHELL wall panel system. Nicknamed The Lotus, the home was completed in 2024 and has already survived two hurricanes – most recently Hurricane Milton. Five additional homes are currently under construction, and another 9,000-square-foot house just landed a permit.
“We’ve brought composites into the architectural, engineering and construction (AEC) industry in market segments where they’ve never been used before, primarily high-rise curtain wall systems and modular units for military purposes and data centers,” says Paul Inglese, CEO of Northstar Technologies Group. He will share how the company penetrated the AEC industry during his keynote presentation at NAPC.
The wall panels are one component of Northstar’s composite building system for residential and commercial markets, which also includes GFRP floor and roof trusses, framing and decking. EXOSHELL panels weigh approximately 5 to 10 pounds per square foot compared to precast concrete, which could weigh 70 to 75 pounds per square foot. In addition, the panels incorporate Owens Corning insulation products – Thermafiber® FireSpan® 40 in the core and Thermafiber RainBarrier® continuous insulation between the wall panel and decorative rainscreen cladding – creating an effective R-value of 29.5.
“One of the big problems in construction has been how to stop thermal massing and thermal bridging,” says Inglese. “Concrete heats up and heats the inside of the building. Steel and aluminum transfer heat or cold back to the building structure. Our FRP curtain wall is thermal neutral.”
Along with the wall panel system for residential and commercial buildings, Northstar Technologies Group also manufactures modular units, including a blast and ballistic resistant, mobile modular system for the military.
“In addition to modular units, we offer a panelized knock-down system that includes four fully assembled walls, floor and roof panels that are structurally engineered to be stacked and can be deployed to remote areas where military personnel can assemble them very quickly,” says Inglese.
Northstar also developed a 55-foot-long, 12-foot-wide, 12-foot-tall FRP modular data center that helps eliminate inefficient thermal massing issues.
“The servers inside data centers generate massive amounts of heat, and you have heat gain from the ambient temperature outside. That’s a bad combination and requires very large HVAC units,” says Inglese. “Our composite floor, wall and roof structure reduces weight and heat gain. From a standpoint of longevity – especially in harsh coastal areas – they outperform any existing modular data center, lowering maintenance costs over the life of the structure.”
Another product line offered by Northstar is its SOLARGLAS pultruded composite columns and trusses for solar parking canopies, utility-grade ground structures and rooftop systems. They can withstand HVHZ locations, as well as snow loads of 60 pounds per square foot, according to the company. The racking systems support a maximum of 64 solar panels per section, eight high by eight across.
A primary reason for Northstar’s success in the AEC industry is it offers services from pre-design through engineering, manufacturing and installation. The company employs architects, structural engineers, product engineers and others to work hand-in-hand with developers and end-use customers.
Company: CarbonTT
Market: Transportation
Carbon Truck & Trailer GmbH (CarbonTT) produces multiaxial, pultruded CFRP components for the automotive industry, including passenger cars and commercial vehicles. The company focuses on two primary product types – structural profiles and energy absorbers.
Structural profiles include chassis beams for trucks and commercial vehicles, as well as stiffeners that can be integrated in the body in white of passenger cars or used within battery casings of electric vehicles (EVs). One of CarbonTT’s notable projects is the CFRP chassis for the Mercedes-Benz Sprinter light commercial vehicle, which has a 1.45-kilogram payload and 4% to 6% fuel and CO2 reduction per vehicle.
CarbonTT designs and fabricates energy absorbers for truck ladder frame chassis and passenger car side rockers. These energy absorbers are particularly important for EVs because batteries increase the vehicle weight.
“It is really crucial to protect both the battery as well as passengers from side impacts because the crash energies are higher with the higher mass of the vehicle,” says Gerret Kalkoffen, managing director and CEO of CarbonTT. “Today, there are quite heavy and expensive aluminum structures within side rockers. We’ve developed an energy absorber in pultruded composite material that has the potential to reduce the weight by 80%.”
CarbonTT initially manufactured CFRP components using vacuum infusion, then considered switching to resin transfer molding. However, the parts it produces for commercial vehicles are quite long – 20 feet or longer for truck chassis. Pultrusion was the best option to manufacture long, strong, lightweight components.
“We are not aware of any other process that produces composite parts as cost-effectively as pultrusion,” says Kalkoffen. However, he acknowledges the limitations of pultrusion: Profiles must be straight and uniformly thick, even if loads vary within the part.
“Pultrusion is usually done with unidirectional roving. But we produce structural parts with a torsional load that requires some kind of fiber lay-up to ensure there is a crushing property and the part doesn’t buckle or break away,” says Kalkoffen. “So, all of our parts have a multiaxial fiber reinforcement.”
CarbonTT developed a patented process for shaping the material to ensure wrinkle-free fabric placement within the die and meet high quality standards required by the automotive industry. It uses highly reactive polyurethane resins and an injection box to enable high-speed production.
“While I am open about the difficulties of the pultrusion process, I want to share optimism about the fact that you can overcome these challenges,” says Kalkoffen. During his presentation at the North American Pultrusion Conference, Kalkoffen will discuss how CarbonTT’s design and quality assessment process help combat potential issues.
“Fabrics have a certain width, and they may be too wide for the die, which leads to wrinkling, or too narrow, which can cause buildup,” says Kalkoffen. “You need to ascertain the design criteria for getting fabrics right if you want to use them in pultrusion.”
Industry collaboration is also key to success, he adds. CarbonTT is partnering with AOC on an energy absorber for a U.S. client that can be integrated into the body in white before it undergoes dip painting, where the part will be subjected to approximately 200 C temperatures for 45 minutes. (AOC will present a session on improved formulations for electrocoating at NAPC.)
“As an industry, we are learning, and there is more and more know-how and experience out there,” says Kalkoffen. “You can be confident that with the right partners you can find a solution somewhat quickly – definitely quicker than in the last decade.”
Market: Fenestration
Marvin Composites (formerly Tecton Products) is part of Marvin, a fourth-generation, family-owned manufacturer of windows, doors and skylights founded in 1912. The company originally made window and door frames out of wood, then later aluminum clad. It added pultruded GFRP into the mix 32 years ago.
The company began by pultruding a patio door sill that required additional strength. It also switched an aluminum windowsill that was experiencing thermal issues to pultruded GFRP.
“We made one or two pultruded components to solve a problem in an existing product line, and it blossomed from there,” says Robb Plagemann, director of advanced research and product development at Marvin Composites. In 1993, the company rolled out its Integrity line, which featured a pultruded structural component with wood cladding on the inside.
“The original Marvin windows we still make are very successful. There’s a lot more flexibility with wood and aluminum than there is with pultrusions,” says Plagemann. “But the Integrity line fits a different niche – a builder-grade window and door system. It has evolved over the years and is now known as the Elevate Collection and the Essential Collection.”
Plagemann cites several advantages to using pultruded components for fenestration products, beginning with strength.
“Our windows go through a lot of wind loading – up to 150 mph winds,” he says. “Pultrusion gives us the required structural performance.” GFRP is also insulating, has a low coefficient of thermal expansion (CTE) and is impact resistant.
Marvin Composites introduced its Modern Collection of pultruded products in 2018. The line features clean lines and large expanses of glass.
“The frames had to be stronger to accommodate the increased glass size, so we developed a new pultruded material incorporating high-density FRP,” says Plagemann. “The material doesn’t quite achieve the stiffness of aluminum, but it’s getting closer to aluminum’s performance levels and it’s also thermally insulating.”
The Modern Collection also features Marvin Connected Home. “The simplest way to describe this smart home automation component is that it allows you to say, ‘Alexa®, open my windows,’” says Emily Chaney, director of enterprise public relations and reputation at Marvin Composites. “All of the components that make that functionality possible are hidden in the pultruded frames, so you don’t see any variation among windows.”
Architects in Sag Harbor, N.Y., opted for Modern fenestration products to create a home with an abundance of light and connection to the outdoors. The home includes 32 windows and two doors, ranging in size from a 33 x 106.5-inch window assembly to a 155 x 108-inch multi-panel door. All the windows and doors feature an ebony exterior finish.
“Black windows on the exterior have become popular in the last few years, but you’re not going to get that color adhesion with a vinyl product,” says Chaney. “You will see fading and chalking happen much more quickly. Pultruded FRP is a great solution for dark colors.”
During his presentation at NAPC, Plagemann will discuss how to leverage pultrusions for enhanced fenestration performance, including achieving fenestration industry standards and providing high-end aesthetics.
“Pultrusion technology enables you to create beautiful products and homes that make people’s lives better,” says Plagemann.
The post Pultrusion Solutions appeared first on American Composites Manufacturers Association.
What's Your Reaction?
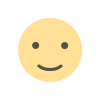
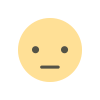
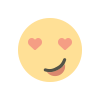
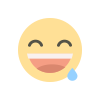

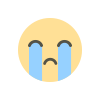
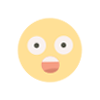