UDRI Engineers Introduced RoboCLASP to Revolutionize Prep of Composite Materials for Bonding
Hand sanding of composite materials in preparation for bonding is labor intensive and hazardous, requiring a delicate touch, a great deal of time, and the use of hazmat suits. A […] The post UDRI Engineers Introduced RoboCLASP to Revolutionize Prep of Composite Materials for Bonding appeared first on American Composites Manufacturers Association.
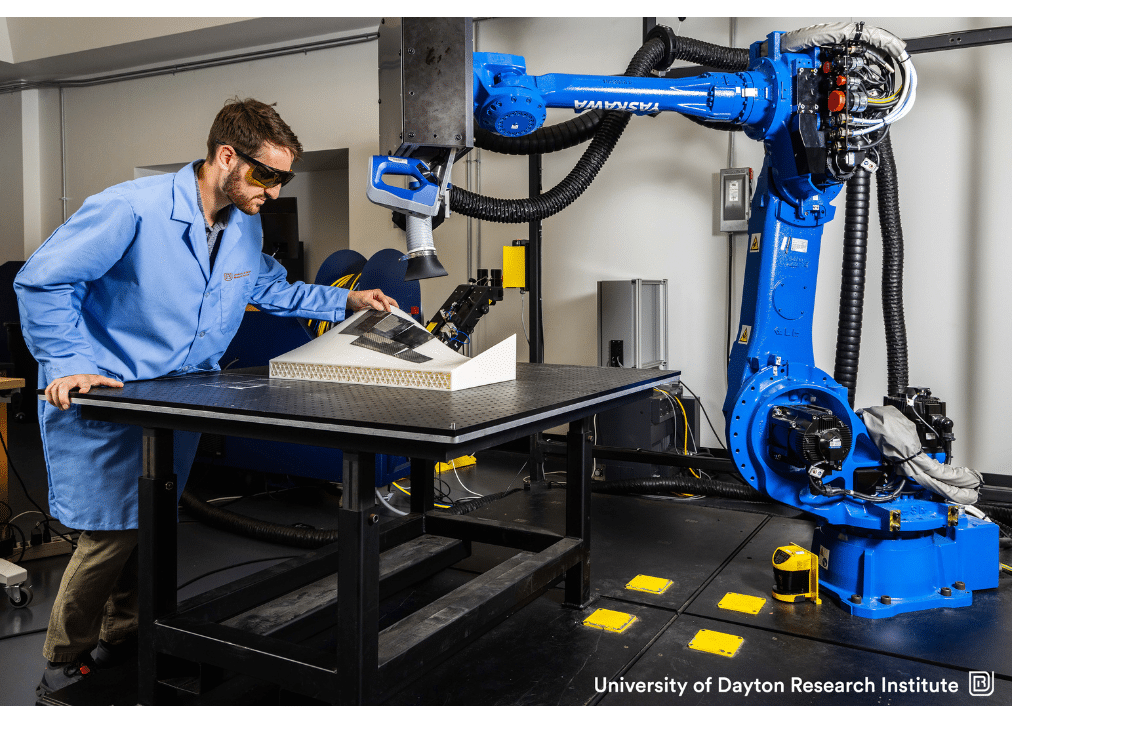
Hand sanding of composite materials in preparation for bonding is labor intensive and hazardous, requiring a delicate touch, a great deal of time, and the use of hazmat suits. A team of engineers from the University of Dayton Research Institute (UDRI), with the support of the U.S. Air Force and partners in the aerospace industry, developed an ultra-fast robotic laser, RoboCLASP, to address these issues faced when using the traditional process of hand sanding polymer matrix composite materials pre-bonding.
CLASP stands for Composite Laser Ablation for Surface Preparation. To remove resin from composites without damaging the materials, RoboCLASP uses athermal ablation, a femtosecond laser process to generate high-energy pulses of light so short that there is no time to generate enough heat to break down the material. The material can then be removed by vacuum filtration.
“Composite Laser Ablation Surface Preparation is the first of many applications we envision for advanced laser manufacturing within the Air Force,” said Adam Hicks, advanced laser manufacturing lead for the Digital Manufacturing and Supply Chain Branch of the Air Force Research Laboratory Materials & Manufacturing Directorate. “CLASP specifically was a reaction to a near-term manufacturing need for the Air Force to reduce the cost and time associated with manual sanding. Working with UDRI, we delivered transitional capability at a speed which I find truly staggering. This is enabled by the willingness and enthusiasm of all of the CLASP partners, but is driven by the innovation and hard work of the technical performers at UDRI.”
The new Rapid Applications of Advanced Manufacturing (RAAM) Laboratory, located in the Dayton Composite Center, was recently dedicated by representatives of the project partners from UDRI, the U.S. Air Force, and the commercial aerospace industry. RoboCLASP is the key technology at the RAAM.
“We’ll also continue to develop the technology in order to expand its applications in advanced manufacturing,” explained Michael Pratt, advanced manufacturing engineer and RAAM team lead. “Our mission at the RAAM lab is to collaborate with all the talented researchers at UDRI to anticipate what our customers’ needs in advanced manufacturing will be in the future, and make sure we’re developing the best solutions now.”
The post UDRI Engineers Introduced RoboCLASP to Revolutionize Prep of Composite Materials for Bonding appeared first on American Composites Manufacturers Association.
What's Your Reaction?
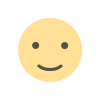
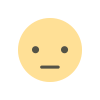
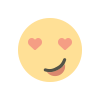
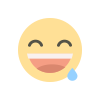

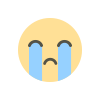
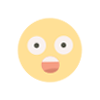