Cummins and Partners Unveil Hydrogen Internal Combustion Engine Innovation with Project Brunel
Advanced Collaboration Leads to Hydrogen Engine Breakthrough Cummins, in collaboration with key tech leaders like Johnson Matthey, PHINIA, and Zircotec,…
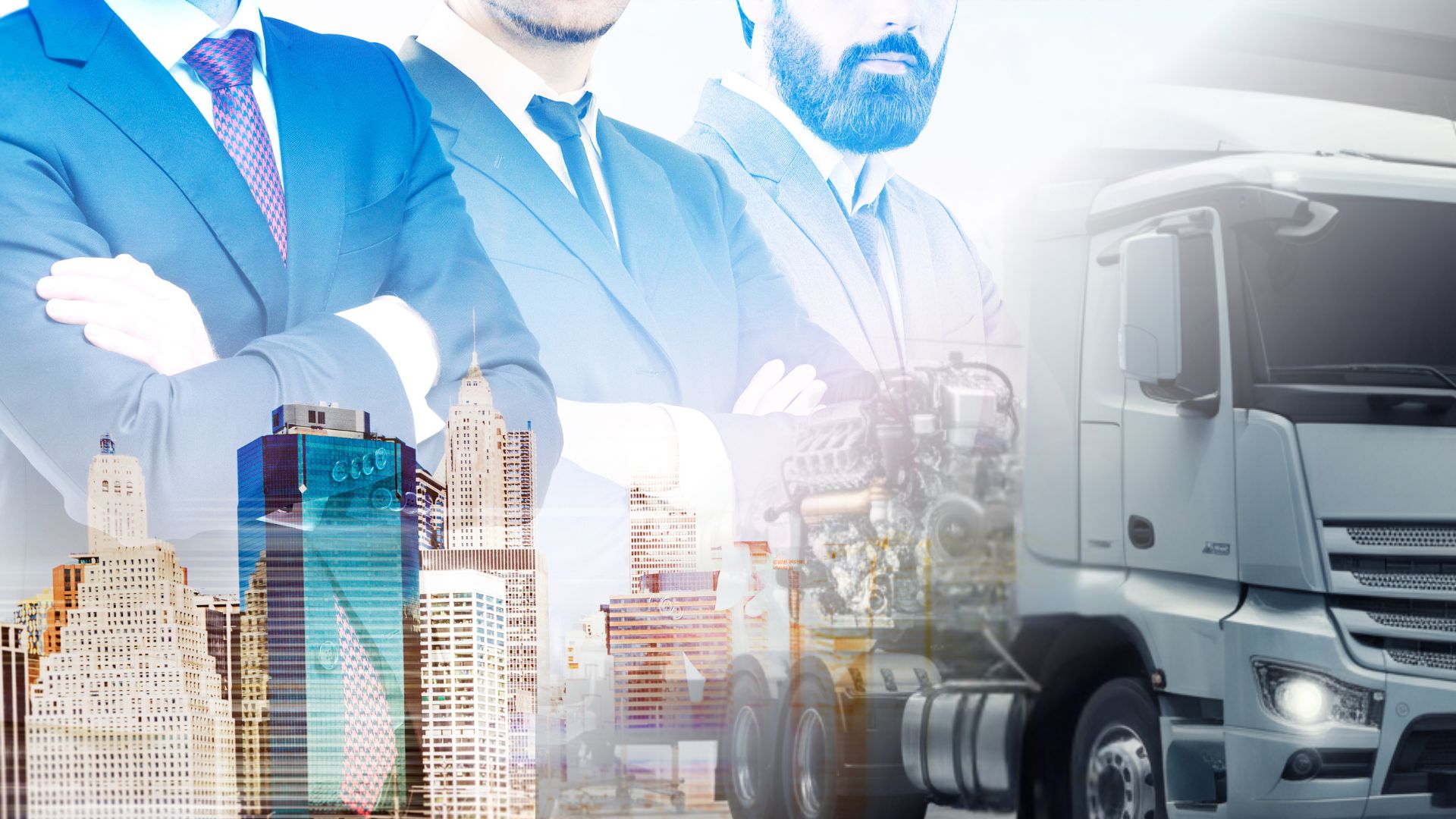
Advanced Collaboration Leads to Hydrogen Engine Breakthrough
Cummins, in collaboration with key tech leaders like Johnson Matthey, PHINIA, and Zircotec, has successfully completed Project Brunel, showcasing a significant leap in hydrogen innovation for commercial vehicles. The project culminated in the development of a 6.7-liter hydrogen internal combustion engine (H2-ICE), which caters to medium-duty trucks, buses, and beyond. This milestone, supported by the UK Government and facilitated by the Advanced Propulsion Centre UK (APC), underlines the potential of zero-carbon hydrogen fuel to reshape the future of transport while addressing performance, durability, and emission challenges.
By using Cummins’ proven engine platform as a foundation, the consortium integrated cutting-edge technologies to make H2-ICE a viable powertrain alternative. This engine drastically reduces tailpipe carbon emissions by more than 99% compared to Euro VI diesel standards and boasts ultra-low nitrogen oxide (NOx) emissions, making it an impactful tool for reducing air pollution.
How Does Hydrogen Internal Combustion Engine Technology Work?
At its core, H2-ICE works like traditional internal combustion engines but instead of diesel or gasoline, it runs on hydrogen fuel. The engine’s complex infrastructure includes hydrogen fuel injection technology developed by PHINIA, a robust after-treatment catalyst system designed by Johnson Matthey, and advanced hydrogen barrier coatings contributed by Zircotec to handle challenges such as ensuring durability under demanding conditions.
One of the most promising aspects of H2-ICE is its ability to seamlessly integrate into current vehicle platforms without requiring a total design overhaul. This approach helps fleet operators transition to cleaner tech with minimal disruption, offering the familiarity of traditional powertrains with a modern, sustainable edge.
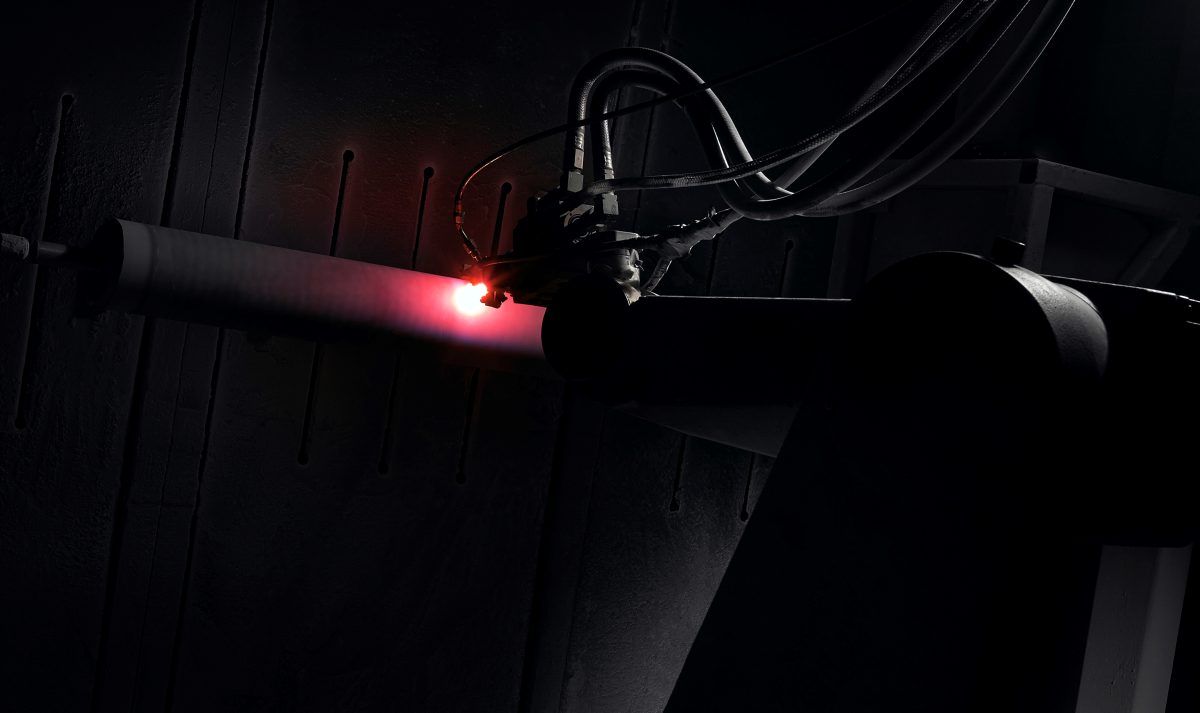
Zircotec plasma applied ceramic coating process
The Role of Ceramic Technology in Hydrogen Barrier Coatings
When it comes to hydrogen internal combustion engines (H2-ICE), like the one developed in Project Brunel, durability and efficiency are critical. This is where ceramic technology steps in, specifically through the hydrogen barrier coatings provided by Zircotec. These coatings play a behind-the-scenes but essential role in enabling hydrogen engines to function reliably under extreme conditions.
Ceramic coatings are like a shield for engine components. They are created by applying a layer of material, often involving advanced ceramics, which can withstand high temperatures, resist wear, and prevent chemical reactions. For hydrogen engines, the stakes are even higher. Compared to traditional fuels, hydrogen burns hotter and faster, and its small molecule size can seep into materials more easily, causing something called “hydrogen embrittlement.” This can weaken engine parts over time, potentially reducing their lifespan.
Here’s where Zircotec’s expertise comes in. Their hydrogen barrier coatings are designed to combat these challenges by creating a protective layer on key engine components. This ceramic-based coating acts as a barrier against hydrogen and other aggressive byproducts of combustion, keeping the underlying materials safe. It ensures that critical parts, like combustion chambers and exhaust systems, don’t degrade or warp under the intense operating conditions of an H2-ICE.
The benefits? First, these coatings help extend the life of engine components, which is a big deal in industries like transportation and construction, where vehicles and equipment are expected to perform for years, sometimes decades. Second, they improve the thermal efficiency of the engine by shielding components from heat loss. This added efficiency translates to better energy use and, ultimately, lower operating costs for fleet operators. Finally, because these coatings enhance durability, they make H2-ICE technology more viable by reducing the likelihood of wear-and-tear issues derailing adoption.
Without these protective layers, the practical use of hydrogen combustion engines would face significant hurdles. Exposed to uncoated conditions, engine parts might fail prematurely, wiping out cost and performance benefits. Ceramic coatings from companies like Zircotec ensure hydrogen engines can meet the reliability standards expected in demanding applications, from medium-duty transit vehicles to heavy-duty agricultural equipment.
This technology demonstrates how cutting-edge materials science is quietly paving the way for clean energy solutions. It’s a fine example of how collaboration across disciplines and industries—as we see in Project Brunel—is addressing the challenges of decarbonization with practical, innovative answers.
Cummins Expands Hydrogen Commitment With New Developments
Project Brunel’s completion isn’t Cummins’ only venture into the hydrogen space. The company is making bold moves to strengthen its hydrogen capabilities. For example, Cummins is currently developing a 15-liter hydrogen engine targeted for heavy-duty applications, including construction and agricultural equipment. This follows an investment of more than £13 million in a new Powertrain Test Facility at its Darlington campus, which supports advanced testing for diesel, hydrogen, natural gas, and battery-electric technologies.
Cummins has also been active globally; in recent news, through its Accelera division, signed a memorandum of understanding with GAIL to collaborate on hydrogen production, blending, transportation, and storage. This partnership aims to accelerate India’s transition to sustainable energy by expanding hydrogen and clean energy infrastructure
Why Hydrogen Matters for Transportation
Why is this development so important? Heavy-duty transport and long-range travel are some of the hardest sectors to decarbonize, given the weight of vehicles and their extended operational demands. While battery-electric vehicles (BEVs) offer strong solutions for light-duty and shorter-range applications, they may not be suitable for everyone due to charging time constraints and weight limitations of batteries.
Hydrogen internal combustion technology carves out a niche by addressing these challenges. Hydrogen fuel is an energy-dense, lighter alternative to battery systems, and it can provide the range and reliability needed for industries like freight, public transit, construction, and agriculture. Additionally, H2-ICE leverages existing internal combustion frameworks, making implementation less costly and faster compared to some alternative clean energy approaches.
Timelines and Market Impact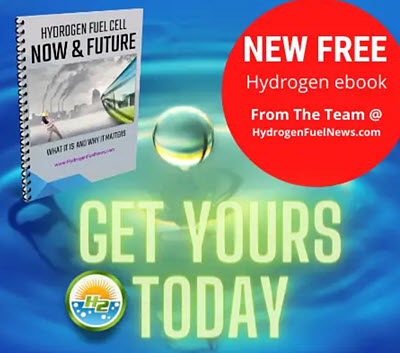
Currently, the scalable design of the 6.7-liter engine developed under Project Brunel paves the way for its adoption in various sectors. While this medium-duty engine is ready to meet near-future demands, the heavy-duty 15-liter variant under development is being positioned for commercial deployment in the next few years, reflecting Cummins’ dedication to boosting the hydrogen ecosystem.
The UK government’s involvement, including investment support from the Department for Business and Trade through the APC, reinforces their bet on hydrogen as a key decarbonization strategy. However, broader market adoption hinges on aligning international regulatory policies to encourage investment in hydrogen-compatible vehicles.
How Can We Use This Technology Now?
The beauty of H2-ICE lies in its versatility and how it leverages our existing automotive infrastructure. Right now, fleet operators can work with manufacturers to explore medium-duty applications of hydrogen technology in public transit and delivery operations. For cities battling poor air quality, transitioning buses to H2-ICE would have real, measurable impacts on reducing emissions without waiting for completely new vehicle models to be rolled out.
Looking further ahead, as heavy-duty versions of this technology mature, industries reliant on powerful machinery, such as agriculture and construction, will have greener options to maintain productivity. Integrating H2-ICE into these sectors will also help build momentum for hydrogen fueling infrastructure, which remains a key enabler in the hydrogen economy’s success.
What's Your Reaction?
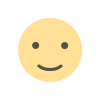
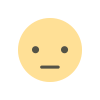
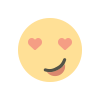
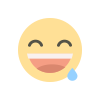

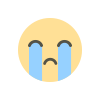
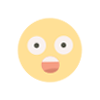